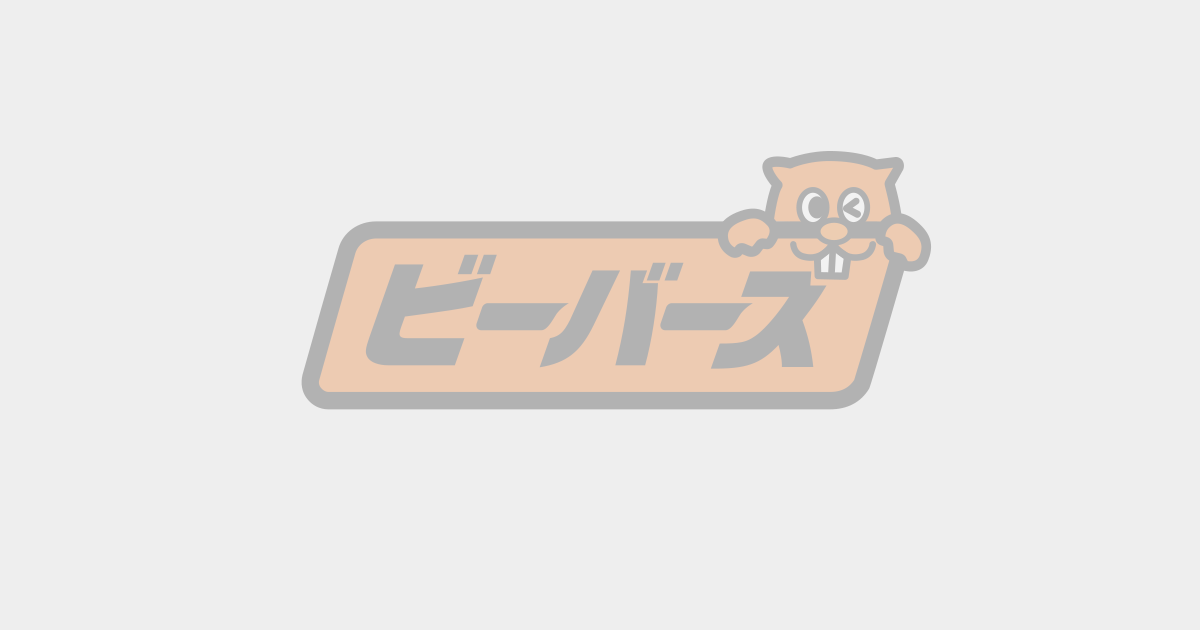
製造業における不良の原因と対策、発生率を低減させる具体的な施策を解説
製造業において、不良品の発生は品質低下とコスト増加につながる重大な課題です。
そこで、不良の原因を特定し、適切な対策を講じることで、製品の品質向上と生産性の改善を実現可能です。
本記事では、製造業における不良の主な原因を解説するとともに、効果的な対策方法を紹介します。さらに、不良率を低減させるための具体的な施策や、先進的な取り組み事例についても詳しく解説しますので、ぜひ参考にしてください。
製造業における不良発生の主な原因
5M+1E分析による不良要因の特定
製造業における不良発生の要因を特定するために、5M+1E分析が活用されます。
これは、5M(Man・Machine・Material・Method・Measurement)に加え、E(Environment)の影響も考慮し、原因を徹底的に分析する手法です。
例えば、作業員の技術不足(Man)や設備の老朽化(Machine)、原材料の品質変動(Material)などが不良の要因となることがあります。これらを特定し、適切な対策を講じることで不良率を低減可能です。
全体を体系的に見直し、各要素を継続的に改善することが、品質向上のポイントです。
ヒューマンエラーと作業工程の確認不足
ヒューマンエラーは、製造業の不良発生における大きな要因のひとつです。なぜなら、誤った作業手順や確認不足が原因となり、品質のばらつきや欠陥品の発生につながることがあるからです。
例えば、作業マニュアルの遵守が不十分だったり、必要なチェック工程が抜け落ちると、ミスが生じる可能性が高まります。これを防ぐためには、標準作業手順の確立、定期的な教育・訓練の実施、ダブルチェック体制の導入などが重要です。
ヒューマンエラーをゼロにすることは難しいですが、仕組みで防ぐことができれば、品質の安定性を確保しやすくなります。
設備・機械の不具合と保守管理の重要性
製造設備や機械の不具合も、不良が発生する大きな要因です。故障や摩耗によって製品品質が低下し、最悪の場合は生産ラインの停止にもつながる可能性があります。
このような問題を防ぐためには、予防保全の考え方が重要です。定期点検を行い、異常を早期に検知することで、急な故障を防ぐことができます。また、設備の適切なメンテナンスを行うことで、製品品質の安定化や稼働率の向上を図ることができます。
設備の状態を常に把握し、適切に管理することで、生産効率と品質の両立が可能です。
不良率改善のための効果的な対策
作業の標準化とマニュアル整備
不良率を改善するためには、作業の標準化が不可欠です。標準化された作業手順を確立することで、ミスの発生を抑え、一貫した品質を維持できます。
具体的には、詳細な作業マニュアルを作成し、誰でも同じ手順で作業ができる環境を整えることが重要です。また、定期的なマニュアルの見直しと改善を行うことで、最新の生産状況に対応しやすくなります。
標準化された作業は、新人教育をスムーズにするだけでなく、属人的な作業を減らし、品質の安定化に大きく貢献します。
教育体制の強化と従業員のスキル向上
作業者のスキル向上は、不良率の低減に直結する重要な要素です。従業員が製造工程や品質管理の重要性を理解し、適切に作業を行うことで、不良の発生を防ぐことができます。
そのためには、定期的な研修や技術指導の実施が欠かせません。OJT(オン・ザ・ジョブ・トレーニング)を活用し、実際の作業現場で学ぶ機会を増やすことも効果的です。
また、ベテラン作業者によるノウハウの共有や、スキル認定制度の導入を通じて、従業員のモチベーションを高めることができます。
教育の強化によって作業精度が向上し、結果的に不良率の改善につながります。
品質管理システムの導入とデータ分析
品質管理システムを導入することで、リアルタイムで不良要因を分析し、迅速な対応が可能となります。なぜなら、IoT技術やAIを活用したデータ収集を行い、不良発生のパターンや傾向を把握することで、原因の特定と対策の立案がスムーズに進むからです。
例えば、生産ラインのセンサーからデータを収集し、異常値を検出することで、不良品を未然に防ぐことができます。また、分析結果をフィードバックし、作業手順の改善や設備のメンテナンス計画に反映させることで、より効果的な品質管理を実現可能です。
データを活用したアプローチは、長期的な品質向上とコスト削減に大きな効果をもたらすでしょう。
不良率を低減させる具体的な施策
自動化・ロボット化による人為的ミスの削減
生産工程の自動化・ロボット化を進めることで、人的ミスの発生を大幅に削減できます。特に、高精度が求められる工程では、AIやロボットを活用することで作業の均一性を確保し、不良品の発生を防ぐことが可能です。
例えば、検査工程に画像認識技術を導入すれば、目視検査の誤判定を防げます。さらに、自動化によって作業者の負担が軽減され、集中力の低下によるミスも抑制できます。
適切な自動化の導入は、生産効率と品質向上を両立するための重要な取り組みです。
IoTとAIを活用した異常検知システムの導入
IoTセンサーやAI分析を活用して、製造プロセスの異常をリアルタイムで検知するシステムを導入することが効果的です。
例えば、温度や振動データを収集し、異常値が検出された際に即時警告を発することで、不良の発生を未然に防ぐことが可能です。また、AIの予測分析を活用すれば、設備故障の兆候を事前に察知し、計画的なメンテナンスを行うことでダウンタイムを削減できます。
データを最大限活用することは、品質の安定化とコスト削減に大きく寄与する重要な要素です。
QCサークル活動による現場の意識改革
QCサークル活動(現場の従業員が自主的に品質改善に取り組む小集団活動)を活性化させることは、現場の意識を高め、不良率低減にも貢献します。なぜなら、作業者が自ら問題点を発見し、改善策を提案・実行することで、より現場に根付いた品質改善が可能となるからです。
例えば、定期的なミーティングを開催し、成功事例を共有することで、改善のモチベーションが向上します。また、改善活動を評価し、優れた取り組みを表彰する制度を設けることで、継続的な改善意欲を促進できます。
現場主導の品質向上は、企業全体の生産性向上につながるため、重要です。
弊社は、建設業界特化の総合ソリューション企業として、人材紹介から事業承継型M&A仲介など、経営に関するあらゆるお悩みを解決いたします。
- 即戦力人材紹介・ヘッドハンティング
- 若手高度外国人材紹介
- 事業承継型M&A仲介
- DXコンサルティング
- 採用コンサルティング
- 助成金コンサルティング
どんな些細なことでもお気軽にお問い合わせください。専任のコンサルタントが貴社のお悩みにお答え致します。
不良対策の成功事例
自動車メーカーの作業手順見直しによる品質向上
ある自動車メーカーでは、不良率の削減と組立精度向上を目的に、作業手順の徹底的な見直しを実施しました。具体的には、作業の標準化と視覚的ガイドの導入により、作業ミスの発生を抑えることに成功しました。
また、QCサークル活動を強化し、現場からの改善提案を積極的に採用しています。その結果、組立工程のミスが減少し、品質の安定化が実現しました。
作業手順の最適化は、不良率低減の重要なアプローチであることが分かります。
食品加工業の自動化システム導入による不良率低減
食品加工業においては、人的ミスによる異物混入や重量誤差が大きな課題のひとつです。そこである企業では、生産ラインに自動計量装置と異物検出システムを導入し、不良発生を防ぐ対策を強化しました。
AIを活用したリアルタイム監視により、異常を即座に検出し、迅速な対応が可能となりました。その結果、品質管理の精度が向上し、不良率の大幅な削減に成功しました。
自動化によるリスク低減は、品質保証の重要なポイントであることが分かります。
電子部品メーカーのAI検査システムによる精度向上
ある電子部品メーカーでは、目視検査の限界から、微細な不良を見逃すケースが発生していました。そこで、AIを活用した画像解析システムを導入し、検査精度を飛躍的に向上させることに成功しました。
これは、AIが膨大な過去データを学習し、異常検出の精度を高めたことで、従来の目視では判別できなかった不良を自動検出できるようになったからです。その結果、製品の品質向上と検査コスト削減が達成されました。
このように、AI技術の活用は、今後も重要な取り組みとなるでしょう。
弊社は、建設業界特化の総合ソリューション企業として、人材紹介から事業承継型M&A仲介など、経営に関するあらゆるお悩みを解決いたします。
- 即戦力人材紹介・ヘッドハンティング
- 若手高度外国人材紹介
- 事業承継型M&A仲介
- DXコンサルティング
- 採用コンサルティング
- 助成金コンサルティング
どんな些細なことでもお気軽にお問い合わせください。専任のコンサルタントが貴社のお悩みにお答え致します。
継続的な品質改善とPDCAサイクルの重要性
不良発生状況の可視化と分析
品質改善の第一歩は、不良発生状況を明確に把握し、データをもとに分析することです。IoTセンサーや品質管理システムを活用し、リアルタイムで不良発生の傾向を可視化することで、根本原因の特定が容易になります。例えば、発生頻度や影響範囲を分析することで、特定の工程に問題があるかを判断できるようになります。
データを活用した不良分析は、感覚的な対応ではなく、根拠のある改善策を導き出せるため、継続的な品質向上に欠かせない取り組みです。
改善計画の立案と実行
分析結果に基づき、具体的な改善計画を立案し、現場で実行に移すことが重要です。改善策には、作業手順の最適化、設備の更新、教育の強化などが含まれます。
例えば、誤作業が多発する工程では、チェック体制を強化することでミスを削減できます。また、改善活動の責任者を明確にし、スケジュールを設定することで、計画的な品質向上が可能です。
改善策は現場の意見を取り入れ、現実的かつ効果的なアプローチを採用することが大切です。
結果の検証と更なる改善策の策定
改善策を実施した後は、結果を検証し、効果を評価することが重要です。不良率の変化や生産効率への影響をデータで確認し、必要に応じてさらなる改善策を策定します。
PDCAサイクルの「Check」と「Act」の段階では、改善が持続可能なものかを判断し、次のステップに進む基準を設けることが求められます。
効果が不十分であれば、原因を再分析し、新たな施策を導入することで、品質向上のプロセスを絶えず進化させることが可能です。
弊社は、建設業界特化の総合ソリューション企業として、人材紹介から事業承継型M&A仲介など、経営に関するあらゆるお悩みを解決いたします。
- 即戦力人材紹介・ヘッドハンティング
- 若手高度外国人材紹介
- 事業承継型M&A仲介
- DXコンサルティング
- 採用コンサルティング
- 助成金コンサルティング
どんな些細なことでもお気軽にお問い合わせください。専任のコンサルタントが貴社のお悩みにお答え致します。
作業環境の整備と従業員教育の重要性
集中しやすい作業環境の構築
作業の効率と品質を向上させるためには、従業員が集中しやすい環境を整えることが重要です。例えば、作業スペースの整理整頓を徹底し、必要な工具や部品をすぐに取り出せるようにすると、作業の無駄を削減できます。
また、適切な照明や騒音対策を行い、作業者が快適に作業できる環境を作ることも大切です。さらに、作業負荷の分散や適切な休憩時間を確保することで、疲労によるミスを防ぎ、品質の安定化につながるでしょう。
定期的な訓練と技能向上プログラムの実施
従業員のスキル向上は、不良率低減のために不可欠です。定期的な研修を実施し、品質管理の基本や最新の技術を習得することで、作業精度の向上を図ることができます。特に、実践的なトレーニングを取り入れることで、現場での適用力が高まります。
例えば、OJT(オン・ザ・ジョブ・トレーニング)を活用し、実際の作業工程で学ぶ機会を増やすと効果的です。スキルアップの機会を提供し続けることで、従業員の成長を促し、品質管理の向上にもつながります。
コミュニケーション促進による問題の早期発見
現場で発生する問題を早期に発見し、迅速に対応するためには、従業員同士のコミュニケーションを活性化させることが重要です。例えば、定期的なミーティングや意見交換の場を設けることで、課題や改善点が共有されやすくなります。
また、現場からのフィードバックを積極的に収集し、管理側と連携することで、適切な対策が迅速に実施できるでしょう。オープンな職場環境を醸成することで、問題解決のスピードが上がるだけでなく、品質向上にも貢献します。
弊社は、建設業界特化の総合ソリューション企業として、人材紹介から事業承継型M&A仲介など、経営に関するあらゆるお悩みを解決いたします。
- 即戦力人材紹介・ヘッドハンティング
- 若手高度外国人材紹介
- 事業承継型M&A仲介
- DXコンサルティング
- 採用コンサルティング
- 助成金コンサルティング
どんな些細なことでもお気軽にお問い合わせください。専任のコンサルタントが貴社のお悩みにお答え致します。
不良率の目標設定と長期的な品質向上戦略
業界標準を考慮した適切な目標値の設定
不良率の改善には、業界標準や競合企業の実績を参考にしながら、現実的かつ挑戦的な目標を設定することが重要です。例えば、業界平均の不良率をベンチマークとして、自社の現状と比較し、達成可能な改善目標を段階的に設定します。
また、顧客要求や市場動向を考慮した品質基準を策定し、継続的に目標値を見直すことで、競争力のある製品品質を維持できます。適切なKPIを設定し、定期的な評価と調整を行うことで、着実な品質向上を図れるでしょう。
関連記事:製造業における不良率の目安とは?不良品が発生する原因と改善方法を解説
中長期的な品質向上ロードマップの策定
品質改善のためには、短期的な対策だけでなく、中長期的なロードマップを策定することが重要です。例えば、1〜3年単位で改善計画を設定し、設備投資、工程改善、教育プログラムの導入を段階的に実施することで、継続的な品質向上を実現できます。
ロードマップには、達成すべき具体的な目標と評価指標を含め、進捗管理を徹底することが不可欠です。このような戦略的な計画により、一時的な品質改善ではなく、長期的な競争力を確保できるしょう。
経営課題としての品質管理の位置づけ
企業全体の視点としては、品質管理を単なる製造現場の課題ではなく、経営戦略の重要な要素として位置づけることが不可欠です。経営層が品質向上に積極的に関与し、品質管理の方針を明確にすることで、組織全体での品質意識が高まります。
例えば、品質目標を経営計画に組み込み、品質改善活動への投資を強化することで、企業のブランド価値向上にもつながります。
品質管理を経営視点で捉え、全社的な取り組みとして推進することは、持続的な品質向上と顧客満足度の向上を実現するうえで不可欠な要素なのです。
ビーバーズでは、製造業に関するさまざまな課題のを解決するためのソリューションを提供しています。
もし、自社で解決できない問題を抱えておられる場合には、下記の申し込みフォームからお気軽にご相談ください。貴社のお役に立つ解決策を、迅速に提案いたします。