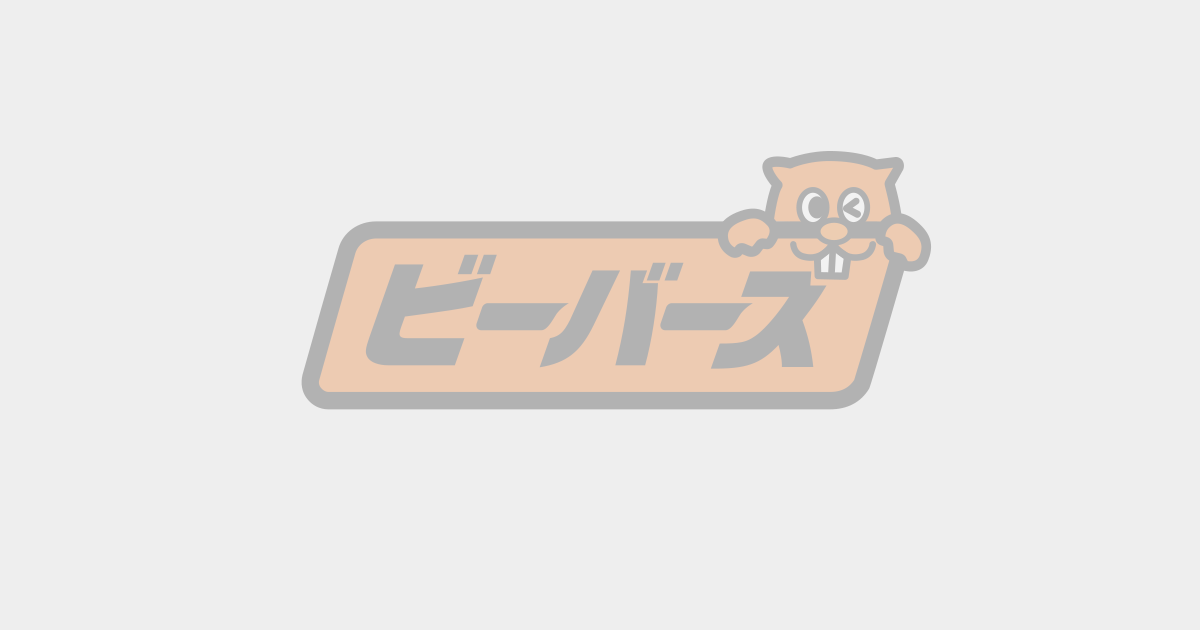
製造業における不良率の目安とは?不良品が発生する原因と改善方法を解説
製造業において、不良率の管理は、品質向上とコスト削減の要となる重要な要素の一つです。
不良率の目安は、一般的に3シグマ(99.7%)〜6シグマ(99.9997%)とされていますが、業種や製品によって適切な目標値は異なります。
また、不良品の発生原因としては、作業ミスや設備の不具合、材料不良などが挙げられるため、さまざまな視点から管理することが重要です。
そこで本記事では、製造業における不良率の目安を解説するとともに、不良品が発生する主な原因と効果的な改善方法について詳しく紹介しますので、ぜひ参考にしてください。
製造業における不良率の基本概念
不良率の定義と計算方法
不良率とは、製造された製品のうち、不良品の割合を示す指標です。
一般的に、不良率は次の式で算出できます。
- 不良品数÷総生産数×100(%)
不良率が高いと、品質問題が多発し、コスト増加や顧客満足度の低下につながります。
製造業では、歩留まりを向上させるために、不良品発生の要因分析や品質改善活動を継続的に実施することが重要です。
不良率の低減を目指すために、生産プロセスの最適化が重要視されています。
PPM(Parts Per Million)の意味と算出方法
PPM(Parts Per Million)とは、不良率をより精密に表すために使用される指標で、100万個当たりの不良品数を示します。
計算式は次の通りです。
- 不良品数÷総生産数×1,000,000
PPMは、通常の不良率(%)よりも細かい単位で品質評価が可能です。
PPMは、微細な品質管理が必要な半導体や精密機器などの業界で活用されており、製造プロセスの信頼性を数値的に評価する際の重要な指標となっています。
不良率とPPMの関係性
不良率とPPMは、どちらも品質管理のための指標ですが、単位の違いによって適用範囲が異なります。
例えば、不良率1%は「1万PPM」に相当し、PPMを用いることで品質管理をより詳細に評価できます。
一般的に、高品質を求められる製品ほどPPM基準が厳しくなり、数十PPM以下が求められるケースも少なくありません。
不良率とPPMを併用することで、製造業は品質改善の進捗を定量的に管理し、最適な生産体制を構築できるでしょう。
製造業で目指すべき不良率の目安
3シグマ(99.7%)の意味と適用分野
3シグマとは、統計学的な品質管理の手法であり、平均値±3標準偏差の範囲に99.7%のデータが収まることを意味します。
これは一般的な品質管理の基準として採用されており、製造業では不良品率を0.3%以下に抑える目標として設定されることが多いです。
特に、消費財や標準的な工業製品などの分野では、3シグマの品質管理が適用され、許容可能な範囲内での品質保証を行うことが求められます。
6シグマ(99.9997%)の重要性と適用例
6シグマは、3シグマよりも厳格な品質管理基準であり、不良品率を100万分の3(3.4PPM)以下に抑えることを目指します。これは、高精度が要求される半導体や航空機部品、医療機器などの製造業で重要視されます。
特に、安全性が最優先される業界では、6シグマを採用することでリスクを最小限に抑え、安定した品質を確保しています。
また、プロセスの最適化と継続的改善を組み合わせることで、無駄を削減し、コスト競争力を強化することにもつながります。
業種別の適切な不良率目標設定
業種によって適切な不良率の目標は異なります。例えば、食品や日用品では、消費者の安全を守るために0.5%以下の不良率を目標にすることが一般的です。
一方、自動車業界や電子部品製造では、より厳密な品質管理が求められ、10PPM以下が目標となることが多いです。
さらに、医療機器や航空宇宙産業では、6シグマに準拠した極めて低い不良率(数PPM以下)が必要とされます。
業界ごとの品質基準を考慮しながら、適切な管理体制を構築することが重要です。
製造現場で不良品が発生する主な原因
ヒューマンエラーによる不良発生
製造現場では、作業者のミスによる不良品発生が大きな課題です。手順の誤りや操作ミス、注意不足によって規格外の製品が生じることがあるからです。特に、経験の浅い作業者や複雑な工程では、ミスの発生確率が高まります。
これを防ぐためには、作業手順の標準化や熟練者による教育・指導が重要です。さらに、AIや自動化技術を導入することで、人為的なミスを削減し、品質の安定化を図ることができます。
設備の不備や故障による影響
製造設備の故障や不具合は、品質低下の大きな要因です。機械の摩耗やメンテナンス不足が原因で、寸法誤差や加工不良が発生しやすくなります。
また、突発的な故障は生産ラインの停止を招き、納期遅延につながることもあります。これを防ぐためには、定期点検や予防保全の徹底が必要です。
さらに、IoT技術を活用し、設備の稼働状況をリアルタイムで監視することで、異常を早期に検知し、故障のリスクを低減できます。
材料不良がもたらす品質低下
使用する原材料の品質が低い場合、製品の品質にも直接影響を及ぼします。例えば、強度不足の素材を使用すると、耐久性が低下し、製品寿命が短くなる可能性があります。
また、材料の成分ばらつきや不純物混入が原因で、製造工程で予期せぬ不良が発生することもあるでしょう。これを防ぐためには、厳格な受入検査を実施し、信頼できる供給元との取引を確保することが重要です。
品質保証体制を強化することで、安定した生産を維持できます。
作業環境や工程設計の問題点
作業環境や工程設計が適切でない場合、不良品の発生率が高まります。例えば、照明が不十分で作業者が細かい欠陥を見逃したり、動線が悪く作業ミスが発生することがあるでしょう。また、工程設計が不適切であると、作業のバラつきが大きくなり、品質が安定しない可能性があります。
これを改善するには、現場の作業環境を見直し、効率的な動線設計を行うことが有効です。さらに、AIやシミュレーションを活用し、最適な生産フローを構築することが品質向上につながります。
弊社は、建設業界特化の総合ソリューション企業として、人材紹介から事業承継型M&A仲介など、経営に関するあらゆるお悩みを解決いたします。
- 即戦力人材紹介・ヘッドハンティング
- 若手高度外国人材紹介
- 事業承継型M&A仲介
- DXコンサルティング
- 採用コンサルティング
- 助成金コンサルティング
どんな些細なことでもお気軽にお問い合わせください。専任のコンサルタントが貴社のお悩みにお答え致します。
不良率を改善するための効果的な対策
教育体制の整備と従業員のスキル向上
不良率を改善するためには、従業員のスキル向上が不可欠です。定期的な研修やトレーニングを実施し、品質管理や作業手順の理解を深めることで、ミスの発生を抑えられます。
特に、新入社員への教育強化や、ベテラン技術者による指導の仕組みを整備することが重要です。また、最新技術を活用したシミュレーションやVRトレーニングを導入することで、実践的な学習環境を構築し、従業員の熟練度向上を図れます。
作業手順の標準化とマニュアル整備
作業手順の標準化を進めることで、工程ごとのバラつきをなくし、不良品の発生を抑えることができます。標準作業手順書(SOP)を作成し、従業員全員が統一されたルールのもとで作業できるようにすることが重要です。
さらに、定期的なレビューを行い、現場の変化に応じてマニュアルを更新することで、より実践的で効果的な作業フローを維持できます。デジタル化された作業指示システムを導入すれば、リアルタイムでの改善が可能となります。
品質管理システムの導入と活用
品質管理システムを導入することで、不良発生の要因を可視化し、迅速な改善策を講じることが可能となります。MES(製造実行システム)やERP(統合業務管理システム)を活用し、製造工程ごとの品質データをリアルタイムで分析することで、不良品の発生を予防できます。
また、AIを活用した異常検知システムを導入することで、不良品が発生する前に兆候を捉え、迅速な対策を講じることが可能です。これにより、品質管理の精度と対応速度が向上します。
自動化技術やAI検査の導入効果
不良率の低減には、自動化技術やAI検査の活用が有効です。例えば、AIを用いた画像認識技術を導入すれば、従来の目視検査よりも精密な欠陥検出が可能となります。
また、ロボットによる自動検査システムを構築することで、人的ミスを削減し、品質の安定化が実現します。さらに、機械学習を活用した品質予測を行うことで、不良発生のリスクを事前に検出し、予防的な対応を行うことができるでしょう。
これにより、継続的な品質改善に期待できます。
関連記事:製造業における不良の原因と対策、発生率を低減させる具体的な施策を解説
弊社は、建設業界特化の総合ソリューション企業として、人材紹介から事業承継型M&A仲介など、経営に関するあらゆるお悩みを解決いたします。
- 即戦力人材紹介・ヘッドハンティング
- 若手高度外国人材紹介
- 事業承継型M&A仲介
- DXコンサルティング
- 採用コンサルティング
- 助成金コンサルティング
どんな些細なことでもお気軽にお問い合わせください。専任のコンサルタントが貴社のお悩みにお答え致します。
不良率低減のための工程管理と品質管理
統計的品質管理(SQC)の活用方法
統計的品質管理(SQC)は、製造工程のデータを分析し、品質のばらつきを抑制する手法です。ヒストグラムや管理図を活用することで、不良発生の傾向を可視化し、原因を特定します。さらに、相関分析や回帰分析を用いれば、不良品の発生要因を予測し、事前対策が可能です。
SQCの導入により、品質の安定化を図り、歩留まりを向上させることができます。このように、データドリブンな意思決定を実施することで、製造業の競争力も高まるでしょう。
リアルタイムモニタリングシステムの導入
製造現場にリアルタイムモニタリングシステムを導入することで、品質異常の早期発見と迅速な対応が可能です。IoTセンサーを活用し、製造工程の温度・圧力・振動などのデータを収集・分析することで、異常発生の兆候を検知できます。
クラウドベースの監視システムを導入することで、遠隔地からでもリアルタイムで品質管理が可能となります。これにより、不良品の発生を最小限に抑え、安定した品質保証を実現できるでしょう。
トレーサビリティの確保と不良品の追跡
トレーサビリティを確保することで、不良品の発生原因を特定し、迅速な改善を実施できます。バーコードやRFIDを活用した製品識別管理により、生産履歴の完全な追跡が可能です。
さらに、MES(製造実行システム)を導入すれば、工程ごとの品質データを記録し、不良発生時に即座に問題を特定できます。これにより、リコール対応のスピードを向上させ、品質保証の信頼性を確保することが可能です。サプライチェーン全体の品質管理にも貢献します。
PDCAサイクルによる継続的改善
不良率低減には、PDCA(Plan-Do-Check-Act)サイクルの徹底が重要です。
まず、品質改善の計画を立案し(Plan)、試験導入(Do)を実施しましょう。次に、結果を分析し(Check)、改善策を講じる(Act)ことで、継続的な品質向上が可能となります。
AIやBIツールを活用すれば、改善結果の迅速なフィードバックが可能となり、PDCAのスピードが向上します。これにより、品質管理の最適化と不良率の低減を持続的に実現可能です。
弊社は、建設業界特化の総合ソリューション企業として、人材紹介から事業承継型M&A仲介など、経営に関するあらゆるお悩みを解決いたします。
- 即戦力人材紹介・ヘッドハンティング
- 若手高度外国人材紹介
- 事業承継型M&A仲介
- DXコンサルティング
- 採用コンサルティング
- 助成金コンサルティング
どんな些細なことでもお気軽にお問い合わせください。専任のコンサルタントが貴社のお悩みにお答え致します。
不良率改善の成功事例と具体的な取り組み
自動車業界における6シグマ達成事例
ある自動車メーカーは、6シグマ手法を活用して製造品質の改善を図り、不良率を大幅に低減しました。特に、組立工程において詳細なデータ分析を行い、工程内のばらつきを最小限に抑えることで、99.9997%の品質保証を実現しました。
さらに、AIを活用したリアルタイム監視システムを導入したことで、異常発生を事前に検出できるようになり、迅速な対応が可能となりました。
結果として、リコール件数の削減とコスト削減につながり、競争力の強化を実現しました。
電子部品メーカーの検査工程改善例
ある電子部品メーカーでは、従来の目視検査をAIと画像認識技術に置き換えることで、不良品の検出精度を向上させました。自動検査システムの導入により、微細な欠陥を高精度で識別できるようになり、ヒューマンエラーを大幅に削減できるようになりました。
さらに、検査データをリアルタイムで収集し、統計分析を行うことで、不良発生の要因を特定しやすくなりました。
これにより、品質の安定化とコスト削減を実現し、納品後のトラブル発生率も低下しました。
食品製造業の異物混入防止対策
食品製造業では、安全性確保のために異物混入を防ぐ厳格な品質管理が求められます。ある食品メーカーでは、X線検査機や金属探知機を導入し、異物検出の精度を強化しました。また、作業員の衛生管理を徹底し、異物混入のリスクを最小限に抑える体制を整えました。さらに、IoT技術を活用して製造環境の監視を行い、異常発生時には自動でアラートを発信する仕組みを構築しました。
これにより、異物混入事故の発生を防ぎ、消費者の信頼確保に貢献しました。
中小製造業における低コスト改善策
中小製造業では、大規模投資が難しいため、低コストでの品質改善が重要となります。ある企業では、簡易なデータ収集システムを導入し、現場の作業ミスを分析することで、改善点を洗い出しました。また、標準作業手順書(SOP)の作成と従業員への教育を強化することで、品質管理の精度を向上させることができました。さらに、設備の定期点検を徹底し、故障リスクを低減することで、不良率を削減しました。
これにより、限られた予算の中でも安定した品質を確保し、企業競争力の強化に成功しました。
弊社は、建設業界特化の総合ソリューション企業として、人材紹介から事業承継型M&A仲介など、経営に関するあらゆるお悩みを解決いたします。
- 即戦力人材紹介・ヘッドハンティング
- 若手高度外国人材紹介
- 事業承継型M&A仲介
- DXコンサルティング
- 採用コンサルティング
- 助成金コンサルティング
どんな些細なことでもお気軽にお問い合わせください。専任のコンサルタントが貴社のお悩みにお答え致します。
不良率管理がもたらす経営上のメリット
コスト削減効果と利益率の向上
不良率を適切に管理することで、ムダなコストを削減し、利益率の向上につながります。不良品が発生すると、材料費の損失や再製造の手間が増え、企業のコスト負担が重くなります。これを防ぐために、品質管理を徹底し、予防的な改善策を講じることで、生産効率を向上させることが可能です。さらに、不良率が低減することで顧客クレーム対応や返品コストも削減され、経営の安定化と持続的な成長を支える重要な要素となります。
顧客満足度と企業ブランド価値の向上
不良率の低減は、製品の品質向上につながり、結果として顧客満足度を高める要因となります。高品質な製品を安定して提供できる企業は、信頼性が増し、ブランド価値の向上につながります。
顧客の評価が高まれば、リピート購入や口コミによる新規顧客獲得が促進され、売上向上にも寄与するでしょう。また、品質管理の強化によるリコールリスクの低減や市場評判の向上は、企業の長期的な成長戦略にも貢献します。
競争力強化と市場シェアの拡大
不良率管理を徹底することで、製品の信頼性が向上し、競争力強化につながります。品質の高い製品は価格競争に巻き込まれにくく、顧客の選択肢として優位に立つことができます。また、不良率を低減することで製造コストを抑え、適正価格で市場に投入することが可能となり、シェア拡大のチャンスが広がるでしょう。特に、品質が重視される業界では、優れた品質管理が市場でのポジション確立に大きな影響を与える重要な要素となります。
従業員のモチベーション向上と組織文化の改善
品質管理を強化し、不良率を低減することは、従業員のモチベーション向上にもつながります。作業ミスが減り、生産効率が向上することで、現場のストレスが軽減され、働きやすい環境が整います。また、品質向上を重視する企業文化が定着すれば、従業員の意識が高まり、自発的な改善提案が増えることも期待できるでしょう。結果として、品質意識の高い組織が形成され、企業全体の成長を促す基盤が強化されるのです。
ビーバーズでは、製造業に関するさまざまな課題のを解決するためのソリューションを提供しています。
もし、自社で解決できない問題を抱えておられる場合には、下記の申し込みフォームからお気軽にご相談ください。貴社のお役に立つ解決策を、迅速に提案いたします。