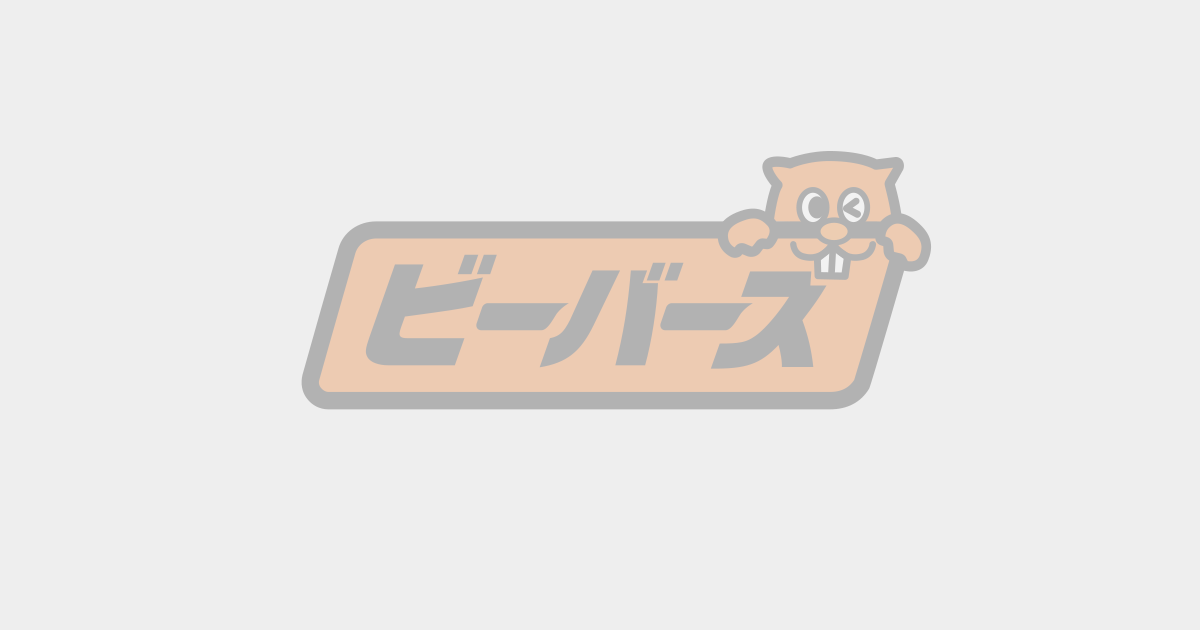
製造業界ごとの原価率の目安とは?改善策やコストが高くなる原因も解説
製造業界における原価率は、企業の収益性を左右する重要な指標です。
そこで本記事では、業界ごとの原価率の目安を詳しく解説し、それぞれの特性に応じた数値を示します。
また、原価率が高くなる原因についても考察し、具体的な改善策を提案しますので、ぜひ参考にしてください。
原価率の基本的な定義と重要性
原価率とは?
原価率とは、製品の原価がその販売価格に対して占める割合を示す指標です。具体的には、製品やサービスを提供するために必要なコストを販売価格で割り、その結果を百分率で表します。
原価率は、企業が製品の収益性を評価し、コスト管理の効率を確認するための基本的な指標です。高い原価率は、利益が圧迫されている可能性を示唆します。
原価率の計算方法
原価率の計算は比較的簡単で、以下の式を使用します。
原価率(%)=(製造原価※÷売上高)×100
※製造原価の計算式は次のとおりです。
製造原価=総製造費用+期首の材料と仕掛品(製造途中の製品)の棚卸高-期末仕掛品と未使用の材料費
なお、総製造費用には、材料費、労務費、経費などが含まれます。
例えば、製品の原価が50,000円で、販売価格が100,000円の場合、原価率は50%となります。この計算により、企業は製品のコストと価格のバランスを把握できます。
ビジネスにおける原価率の重要性
ビジネスにおいて原価率は、収益性とコスト管理の重要な指標です。原価率を定期的に把握することで、企業は製品の収益性を評価し、効率的なコスト管理が可能となります。
原価率の変動を監視することで、製造プロセスや供給チェーンにおける効率の改善点を特定し、適切な戦略を立てることができます。また、競争力を維持するための価格設定やコスト削減の方針を見直す上でも、原価率は重要な指標です。
原価率の最新動向
国内外の原価率トレンドとグローバル比較
近年、日本の製造業では原価率が高止まりする傾向が続いています。背景には原材料価格やエネルギーコストの上昇、為替変動による輸入コスト増加が挙げられます。
グローバルで見ると、海外製品との価格競争が激化し、特に衣服・繊維製品や印刷・製版業では収益性が圧迫される傾向が強まっています。
また、欧米の一部業界ではDXや自動化による原価率低減が進んでいる一方、日本では中小企業を中心にデジタル化の遅れが原価率改善の足かせとなるケースも見られます。
市場環境・規制変化が与える影響
2020年代以降、原材料価格の高騰やエネルギー費の上昇、為替変動、労務費の増加が各業界の原価率に直接的な影響を及ぼしています。
さらに、価格転嫁の難しさや、サプライチェーン混乱、環境規制の強化も原価率上昇の要因です。
中小製造業では、価格転嫁力が大企業より低く、コスト増加を十分に販売価格に反映できない現状が続いています。
今後は、原価計算の精度向上やデジタル化、サプライチェーン全体の最適化が原価率改善のカギとなります。
各製造業界の原価率の目安
以下の表は、一般的な目安を示していますが、個々の企業や製品によって異なる可能性がありますので、あくまでも参考程度にご覧ください。
業界 | 原価率の目安 (%) |
食品製造業 | 75〜80 |
ハイテク製品製造業 | 60〜70 |
医薬品製造業 | 30〜35 |
建設業 | 76〜77 |
自動車製造業 | 80〜85 |
繊維製造業 | 75〜80 |
化学製品製造業 | 70〜75 |
機械製造業 | 75〜80 |
電気機器製造業 | 70〜75 |
金属製品製造業 | 75〜80 |
原価率の目安が示す意味
原価率の目安は、企業のコスト管理や価格戦略において重要な指標となります。適正な原価率を維持することで、利益率を確保しつつ競争力を保つことが可能です。
また、原価率の変動を監視することで、製造コストの削減や効率化の余地を見つけ出すことができます。
さらに、業界平均との比較を通じて、自社の競争優位性を評価する手助けとなるでしょう。
原価率が高くなる主な原因
材料費の高騰
材料費の高騰は、原価率が高くなる主な原因の一つです。原材料の市場価格が上昇すると、製品を製造するために必要なコストが増加します。特に、金属やプラスチックなどの原材料の価格変動が大きい場合、企業はコストの増加に直面します。
これにより、製品の価格設定にも影響を及ぼし、収益性が低下する可能性があるのです。
労働コストの上昇
労働コストの上昇も、原価率の増加に寄与する重要な要素です。労働者の賃金が上昇することや、福利厚生の充実が求められる場合、企業の人件費が増加します。
また、労働市場の状況により、人材確保が困難な場合にはさらに高い賃金を支払う必要があるため、総コストが上昇します。これにより、製品の原価率が高くなるケースも少なくありません。
生産効率の低下
生産効率の低下は、製造コストの増加につながります。例えば、機械の老朽化やメンテナンス不足、作業員のスキル不足などがその原因です。
効率的に生産が行われないと、時間と資源が無駄に使われ、総生産コストが増加します。この結果、原価率が高くなるのです。
在庫管理の不備
在庫管理の不備は、コストの無駄遣いを引き起こす要因です。在庫の過剰保有や不適切な管理によって、保管費用や廃棄ロスが増加します。特に、食品や医薬品などの賞味期限がある製品では、適切な在庫管理が不可欠です。
不適切な在庫管理により、コストが増加し、結果的に原価率が高くなることがあります。
原価率の改善策と効果的な手法
効果的なコスト削減方法
効果的なコスト削減には、まず無駄の削減と効率化が必要です。例えば、材料の適切な管理と使用、エネルギー消費の削減、作業工程の改善などが挙げられます。
定期的なコストレビューとベンチマーク分析も重要で、他社の優れた事例を参考にすることも、自社のコスト削減に役立ちます。
生産プロセスの最適化
生産プロセスの最適化は、製造業の競争力を高めるために不可欠です。具体的には、リーン生産方式やシックス・シグマなどの方法論を導入し、無駄を削減し、生産効率を向上させます。プロセスの標準化と自動化も、品質向上とコスト削減に寄与する重要な要素です。
購買戦略の見直し
購買戦略の見直しも、原価率の改善に大きく寄与します。例えば、サプライヤーの選定と契約条件の見直し、購買品の集中化、ベストプラクティスの導入などが有効です。
市場調査を行い、最適なタイミングでの購買を実施することで、コスト削減が可能です。
技術革新の導入
技術革新の導入は、原価率を大幅に改善する可能性があります。例えば、最新の製造技術や自動化技術の導入により、生産効率が向上し、コスト削減が可能です。また、デジタルツインやIoTを活用することで、リアルタイムのデータ分析と予測が可能となり、プロセスの最適化とコスト削減に繋がります。
原価率改善のための最新DX・自動化事例
IoT・AI活用による生産効率化
製造業ではIoTセンサーやAIを活用した工程の自動化・可視化が進み、生産効率と原価率改善に大きな成果を上げています。たとえば、AIロボットによる検品自動化(日東電機製作所)、IoTによる稼働状況のリアルタイム把握や設備の待機時間・故障時間の最小化(セイブ株式会社)などが代表例です。
これにより、人的作業の削減・品質向上・設備稼働率の最大化が実現し、製造原価の低減と持続的な競争力強化につながっています。
在庫最適化と需要予測の高度化
在庫最適化や需要予測の高度化もDXによる原価率改善の重要なポイントです。生産スケジューラやERP・生産管理システムの導入によって、在庫回転率の向上や余剰在庫・欠品リスクの最小化が可能になります。
また、AIによる需要予測や生産計画の精度向上により、調達コストや在庫コストの削減、納期遵守率の向上といった効果が得られています。これらのシステムは、部門間の情報連携やトラブル対応の迅速化にも寄与します。
デジタルツイン・スマートファクトリーの実践例
デジタルツインやスマートファクトリーの導入は、現場のリアルタイムデータを仮想空間で再現し、最適な生産シミュレーションや設備保全を可能にします。これにより、段取り時間の短縮、不良率の低減、リードタイムの短縮などが実現し、原価率の継続的な低減と生産性向上が図られています。
実際に、DX導入企業では「計画立案工数の40%削減」「生産計画時間の1/4短縮」「現場の要望を反映した柔軟な生産体制」など、デジタル技術による大幅な業務改善が報告されています。
これらのDX・自動化事例は、原価率改善と利益率向上の両立を実現する有効なアプローチとして、今後ますます重要性を増しています。
弊社は、建設業界特化の総合ソリューション企業として、人材紹介から事業承継型M&A仲介など、経営に関するあらゆるお悩みを解決いたします。
- 即戦力人材紹介・ヘッドハンティング
- 若手高度外国人材紹介
- 事業承継型M&A仲介
- DXコンサルティング
- 採用コンサルティング
- 助成金コンサルティング
どんな些細なことでもお気軽にお問い合わせください。専任のコンサルタントが貴社のお悩みにお答え致します。
コスト管理の適切なやり方
定期的なコスト分析
コスト管理の基本は、定期的なコスト分析です。企業は四半期ごとや月次でコストデータを収集し、分析することで、どの部門やプロセスに無駄があるかを特定します。このプロセスにより、迅速な問題解決や改善策の導入が可能となります。また、過去のデータと比較することで、効果的なコスト削減が実現可能です。
KPIの設定とモニタリング
効果的なコスト管理には、KPI(重要業績評価指標)の設定とそのモニタリングが必要です。具体的なKPIとしては、材料費、労働費、製造コストなどが挙げられます。
これらの指標を設定し、定期的に評価することで、コストパフォーマンスの改善状況を把握できるでしょう。また、目標達成度を継続的に監視することで、迅速な意思決定が可能となります。
コスト削減の成功事例
コスト削減の成功事例として、例えばある製造企業では、Lean Six Sigmaの導入により生産プロセスの無駄を排除しました。また、ある食品製造業者は、サプライチェーンの見直しを行い、材料の調達コストを20%削減しました。
これらの事例は、効果的なコスト管理手法を導入することで、顕著な成果を上げることができる例として参考になります。
弊社は、建設業界特化の総合ソリューション企業として、人材紹介から事業承継型M&A仲介など、経営に関するあらゆるお悩みを解決いたします。
- 即戦力人材紹介・ヘッドハンティング
- 若手高度外国人材紹介
- 事業承継型M&A仲介
- DXコンサルティング
- 採用コンサルティング
- 助成金コンサルティング
どんな些細なことでもお気軽にお問い合わせください。専任のコンサルタントが貴社のお悩みにお答え致します。
原価率管理のためのKPIと運用ポイント
原価率以外に重視すべき指標
原価率だけでなく、材料費・労務費・製造経費などのコスト構成要素ごとのKPIを設定することが重要です。加えて、
- 設備稼働率
- 不良率(歩留まり率)
- 工数生産性(労働生産性)
- 製造リードタイム
- 在庫回転率
- 納期遵守率
なども重視すべき指標です。これらを組み合わせて管理することで、現場のムダや改善ポイントを多角的に把握できます。
定期的なコスト分析とPDCAサイクル
KPIを活用した原価管理では、標準原価と実際原価の差異分析を定期的に行い、PDCAサイクルで継続的な改善活動を推進することが不可欠です。
- 月次や四半期ごとにコストデータを集計し、予算や目標値と比較
- 差異の要因を分析し、改善策を立案・実行
- 結果を再評価し、次のアクションにつなげる
こうしたサイクルを定着させることで、利益率向上や経営判断の精度向上につながります。
社内共有・現場巻き込みの工夫
効果的な原価管理には、KPIやコスト情報の「見える化」と現場の巻き込みが不可欠です。
- 製造原価報告書やKPI進捗を定例会議や社内ポータルで共有
- KPIツリーなどを活用し、目標達成のための具体的な行動指標を現場レベルまで分解
- 現場担当者の意見やアイデアをKPI設定や改善策に反映し、主体的な改善活動を促進
このような運用により、現場のコスト意識が高まり、全社一体での原価率改善が実現します。
弊社は、建設業界特化の総合ソリューション企業として、人材紹介から事業承継型M&A仲介など、経営に関するあらゆるお悩みを解決いたします。
- 即戦力人材紹介・ヘッドハンティング
- 若手高度外国人材紹介
- 事業承継型M&A仲介
- DXコンサルティング
- 採用コンサルティング
- 助成金コンサルティング
どんな些細なことでもお気軽にお問い合わせください。専任のコンサルタントが貴社のお悩みにお答え致します。
原価率・コスト管理に関するよくある質問Q&A5選
Q1.原価率とは何ですか?どのように計算しますか?
A.原価率とは、売上高に対する原価(コスト)の割合を示す指標です。計算式は「原価÷売上高×100(%)」です。原価率を把握することで、利益率やコスト管理の効率性を評価できます。
Q2.原価率が高くなる主な原因は何ですか?
A.原価率が高くなる主な原因は、仕入れコストの上昇、原材料価格の変動、廃棄ロスの増加、販売価格の設定ミス、生産プロセスの非効率化などが挙げられます。
Q3.原価率を下げるためにはどんな方法がありますか?
A.原価率を下げるには、廃棄ロスの削減、仕入先や原材料の見直し、生産プロセスの効率化、在庫管理の最適化、販売価格の適正化などが有効です。コスト削減だけでなく、品質維持にも注意が必要です。
Q4.原価管理を効率よく行うにはどうすればよいですか?
A.標準原価を設定し、実際原価との比較や差異分析を定期的に行うことが重要です。また、原価計算システムや管理ソフトを活用し、材料費・労務費・間接費などのコスト構成要素を細かく把握することで、改善余地を特定できます。
Q5.原価率やコスト管理の効果測定はどのように行いますか?
A.原価率以外にも、粗利率、不良率、設備稼働率、在庫回転率などのKPIを設定し、月次や四半期ごとにコスト分析を実施します。PDCAサイクルを回し、現場と情報共有しながら継続的な改善を図ることが効果的です。
ビーバーズでは、製造業に関するさまざまな課題のを解決するためのソリューションを提供しています。
もし、自社で解決できない問題を抱えておられる場合には、下記の申し込みフォームからお気軽にご相談ください。貴社のお役に立つ解決策を、迅速に提案いたします。