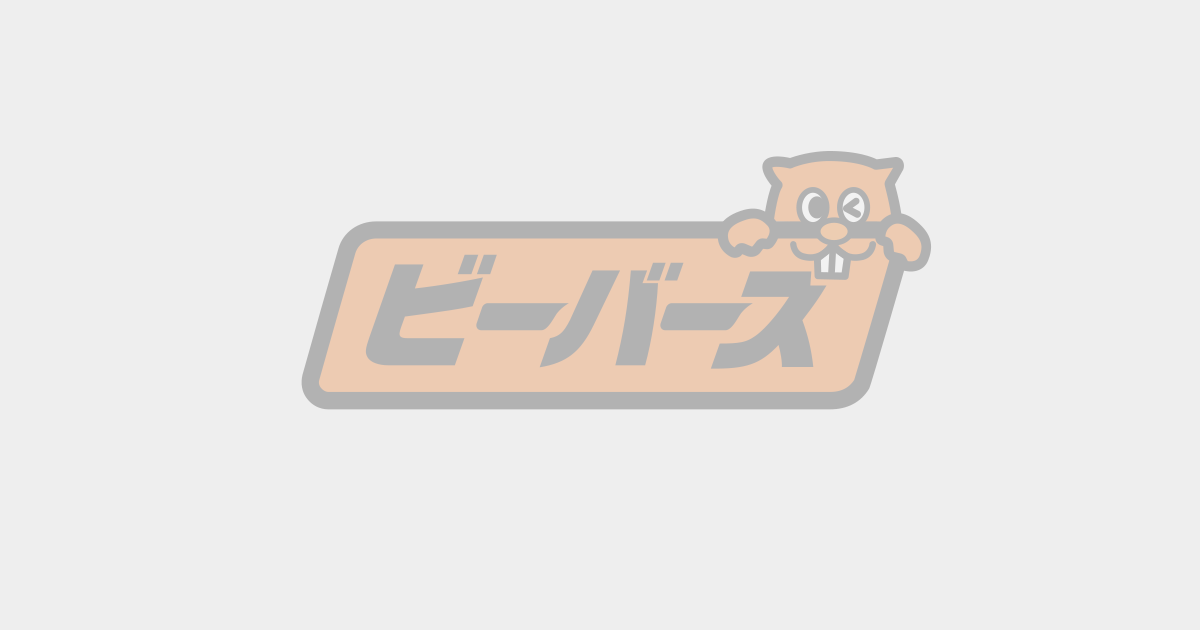
製造業DXとは?導入メリットや成功事例、主な課題と解決方法も解説
製造業におけるデジタルトランスフォーメーション(DX)は、業界の未来を左右する重要な取り組みとして注目を集めています。
そこで本記事では、製造業DXの概念から、その導入によってもたらされるメリット、さらには実際の成功事例まで、幅広く解説します。
また、DX推進において直面する主な課題とその解決方法についても詳しく説明しますので、ぜひ参考にしてください。
製造業DXとは?その重要性も解説
製造業DXの定義
製造業DX(デジタルトランスフォーメーション)とは、デジタル技術を活用して生産プロセスを根本的に改革する取り組みのことです。これにより、データの収集・分析が容易となり、効率的な生産計画や運用が可能となります。具体的には、IoTやAI、ビッグデータなどを活用し、リアルタイムでのモニタリングや予測保守などが行われます。
このような変革により、迅速な意思決定と柔軟な対応が可能となるため、競争力の向上に期待ができるのです。
デジタル技術を活用した生産プロセスの改革
デジタル技術を活用することで、生産プロセス全体の可視化と最適化が可能となります。これは、センサーやIoTデバイスを通じてリアルタイムでデータを収集し、AIがそのデータを分析して予知保全や品質管理を行うからです。
これにより、生産効率の向上とダウンタイムの削減が実現します。
製品の付加価値向上への取り組み
製造業DXは、製品そのものの付加価値向上にも寄与します。例えば、製品にセンサーを組み込み、使用状況データを収集・分析することで、より高品質でユーザーのニーズに応える製品開発が可能です。
製造DXにより、カスタマーエクスペリエンスの向上や、新しいサービスの提供も期待できます。
製造業DXの導入メリット
製造業DXの導入には多くのメリットがあります。以下に主要なメリットを解説します。
業務効率化と生産性向上
デジタル技術を導入することで、手作業の減少やプロセスの自動化が進みます。これにより、業務の効率化と生産性の向上が図れます。
特に、リアルタイムでのデータ収集と分析は、即時の意思決定を支援し、無駄を排除することが可能です。
コスト削減の実現
製造業DXにより、エネルギー消費や材料費の削減が実現します。例えば、AIを活用した予知保全により、故障や異常を事前に察知して対応することで、修理コストや生産停止のリスクを減少させることが可能です。
従業員の安全性向上
デジタル技術の活用により、従業員の安全性も向上します。例えば、IoTデバイスによるリアルタイムの環境監視や、ロボットを用いた危険作業の自動化などが挙げられるでしょう。これにより、労働災害のリスクが低減します。
技術承継の円滑化
製造業DXは、技術承継の面でも大きな効果を発揮します。デジタル技術を活用すれば、熟練工の知識や技能をデータとして保存し、次世代に引き継ぐことが可能です。
これにより、技術の断絶を防ぎ、安定した生産を維持できるようになります。
製造業DXの成功事例
トヨタ自動車|工場IoTによる情報共有基盤の構築
トヨタ自動車は、IoT技術を活用して工場内の設備や機械の情報をリアルタイムで収集・共有する基盤を構築しました。これにより、稼働状況や異常の早期発見が可能となり、生産効率の向上とダウンタイムの削減が実現しました。
さらに、データ分析を通じて予防保全を強化し、品質管理の徹底を図っています。
ダイキン|IoTシステムによる空調機の効率的稼働
ダイキンは、空調機にIoTシステムを導入し、遠隔での監視・制御を可能にしました。これにより、運転状況をリアルタイムで把握し、エネルギー効率の最適化を図るとともに、トラブルの早期発見と迅速な対応が実現しました。
また、データを活用したサービスの提供により、顧客満足度の向上も達成しています。
コマツ|IoT・AIを搭載したスマート建機ソリューション
コマツは、建設機械にIoTとAI技術を搭載し、スマート建機ソリューションを展開しています。これにより、機械の稼働状況や作業効率をリアルタイムで把握し、最適な運用計画を立てることが可能となりました。
さらに、AIを活用した故障予測やメンテナンスの自動化により、コスト削減と生産性向上を実現しています。
パナソニック|生成AIを活用した電気シェーバーのモーター設計
パナソニックは、生成AI技術を活用して電気シェーバーのモーター設計を行い、製品開発の効率化を図っています。
AIが設計プロセスを自動化し、最適な設計パラメーターを生成することで、開発時間の短縮と高性能な製品の提供が可能となりました。また、データ駆動型の設計により、顧客ニーズに即した製品開発を実現しています。
川崎重工|デジタルツインによる工場の生産管理効率化
川崎重工は、デジタルツイン技術を活用し、工場の生産管理を効率化しています。デジタルツインにより、物理的な工場と仮想空間でのシミュレーションを連携させ、稼働状況をリアルタイムで監視・分析することが可能です。
これにより、生産プロセスの最適化やトラブル予測、迅速な対応が可能となり、生産性の向上とコスト削減を実現しています。
上記のように、それぞれの企業が高度な技術を駆使し、生産性や効率の向上を目指しています。
製造業DXの推進ステップ
STEP1|製造現場の理解とDX推進目的の明確化
製造現場の理解は、DX(デジタルトランスフォーメーション)の第一歩です。そこで、現場の業務フロー、設備、技術、働く人々の役割などを詳細に把握することが重要です。その上で、DX推進の目的を明確にします。
例えば、生産効率の向上、品質の改善、新たなビジネスモデルの創出など、具体的な目標を設定します。このステップは、全体の方向性を決定するための基盤となる重要な要素です。
STEP2|課題の明確化とDX戦略の策定
現場の理解をもとに、現状の課題を洗い出し、それに対する解決策を検討しましょう。例えば、生産ラインのボトルネックやデータ管理の問題点などです。そして、これらの課題を解決するための具体的なDX戦略を策定します。
戦略には、技術導入の方針、プロジェクト管理の方法、リソースの割り当てなどが含まれます。戦略は柔軟性を持たせつつ、具体的な成果を目指しましょう。
STEP3|人材確保とツール選定
DXを推進するためには、適切な人材とツールの確保が不可欠です。専門知識を持つ人材の育成や採用を行い、DXの推進体制を整えます。また、具体的なツールの選定も重要です。
例えば、IoTデバイス、ビッグデータ分析ツール、クラウドサービスなど、目的に応じた技術を導入します。これにより、DXの推進をスムーズに行うことができるでしょう。
STEP4|データ収集の実施
製造現場でセンサーやIoTデバイスを活用し、設備の稼働状況や生産データ、品質データなどをリアルタイムで収集します。これにより、現場の状況を詳細に把握し、データに基づいた意思決定が可能となります。
適切なデータの収集は、DXの成功に向けた重要な要素です。
STEP5|DX推進状況の評価と見直し
DXの進捗状況を定期的に評価し、必要に応じて計画を見直しましょう。具体的なKPI(重要業績評価指標)を設定し、目標達成度を測定します。
例えば、生産効率の向上率や、コスト削減率などが評価指標の代表例です。また、現場からのフィードバックを収集し、改善点を洗い出します。
継続的な評価と見直しにより、DXの効果を最大化することが可能です。
製造業DXの主な課題と解決方法
組織の大規模化による新規導入の遅れ
製造業のDX(デジタルトランスフォーメーション)において、組織が大規模になると新しいシステムや技術の導入が遅れることがあります。部署間の調整や承認プロセスが複雑化し、全体のスピードが低下するのが一因です。
解決策としては、導入プロセスを簡略化するためのプロジェクト管理ツールの導入や、トップダウンのリーダーシップを強化し、迅速な意思決定を促すことが有効です。
業務プロセスの複雑化への対応
製造業のDX推進により業務プロセスが複雑化し、従来の作業フローに適応できなくなることも課題の一つとして挙げられます。この問題に対しては、プロセスマッピングを行い、各業務フローの現状と問題点を可視化することで、改善点を明確にすることが重要です。
また、RPA(ロボティック・プロセス・オートメーション)やAIを活用し、業務プロセスの自動化と効率化を図ることが効果的です。
人材育成と技術習得の必要性
新しい技術やシステムの導入に伴い、社員のスキルアップと技術習得が求められるのも課題です。この解決策としては、継続的な教育プログラムの実施や、eラーニングプラットフォームの活用が挙げられます。
また、社内のエキスパートによるトレーニングや、外部専門家を招いたワークショップを開催することで、現場での実践力を高めることが可能です。
投資コストと効果測定の課題
製造業DXには多大な投資が必要であり、そのコストと効果の測定が難しいことも課題となります。解決策としては、初期投資を抑えるためにクラウドサービスの利用や、段階的な導入を計画することが有効です。また、投資対効果を定量的に評価するためのKPI(主要業績評価指標)を設定し、定期的に効果測定を行うことで、投資の妥当性を検証し、必要に応じた見直しを行うことが重要です。
製造業DXの将来展望
AIとIoTの更なる融合
AIとIoT(モノのインターネット)の融合は、製造現場のスマート化を加速させます。
IoTデバイスが収集する膨大なデータをAIが分析することで、設備の故障予測、プロセスの最適化、生産ラインのリアルタイム監視が可能です。この融合により、予防保全やエネルギー効率の向上、労働生産性の向上が実現します。
将来的には、AIとIoTが連携して自己学習し、製造現場の変化に即座に適応する自律的なシステムが普及するでしょう。
デジタルツインの進化と活用拡大
デジタルツインは、物理的な製品やプロセスのデジタルコピーを作成し、シミュレーションや最適化に利用します。これにより、製品設計の段階から生産、メンテナンスまでの全工程を仮想環境で検証できるため、試作コストの削減や市場投入までの時間短縮が図れるでしょう。
今後、デジタルツインの技術はますます進化し、多様な分野での活用が期待されます。例えば、都市計画やエネルギーマネジメントなど、広範な応用が可能です。
メタバースを活用した新たな製品開発と顧客体験
メタバースは、仮想空間を活用した新しいビジネスチャンスを提供します。製造業においても、製品のデザインやプロトタイプの試作、リモートでの製品展示や顧客体験の提供など、多岐にわたる応用が期待されます。
仮想空間での共同作業により、地理的な制約を超えてグローバルなチームが協力し合えるため、革新的な製品開発が進むでしょう。また、顧客がメタバース内で製品を試用し、フィードバックを即座に反映できるため、よりパーソナライズされた製品開発が可能となります。
グローバル競争力強化への貢献
製造業DXは、企業の競争力を国際的に強化する鍵となります。デジタル技術の導入により、生産性の向上、コスト削減、品質の安定化が実現し、グローバル市場での競争力が高まります。また、データ分析とAIを活用することで、市場動向の予測や需要の変動への柔軟な対応が可能となり、顧客ニーズに迅速かつ正確に応えることが可能です。さらに、持続可能な生産と環境負荷の軽減を追求することで、企業の社会的責任(CSR)も強化され、国際的な信頼を獲得する要因となります。
製造業DXのまとめ
このように、製造DXを推進するには、さまざまな取り組みによる課題の解決が必要です。
そこで、製造DXにお悩みのある方は、今すぐビーバーズにご相談ください。
ビーバーズは製造業DXに関する豊富な知識と経験を持つコンサルティング企業です。
ビーバーズは製造業特有の課題を深く理解し、効率化、生産性向上、コスト削減などの具体的なメリットを提供します。
さらに、現場主導で低コストなDX実現をサポートし、SaaS活用による柔軟な解決策も提案可能です。
ビーバーズは、企業の個別ニーズに合わせた戦略立案から実装まで、包括的なサポートを提供し、製造業のデジタル変革を成功に導く強力なパートナーです。
下記のフォームより、無料相談の申し込みができますので、ぜひご活用ください。